

Stampers produced from the mothers after separating were chrome plated to provide a hard stain-free surface.
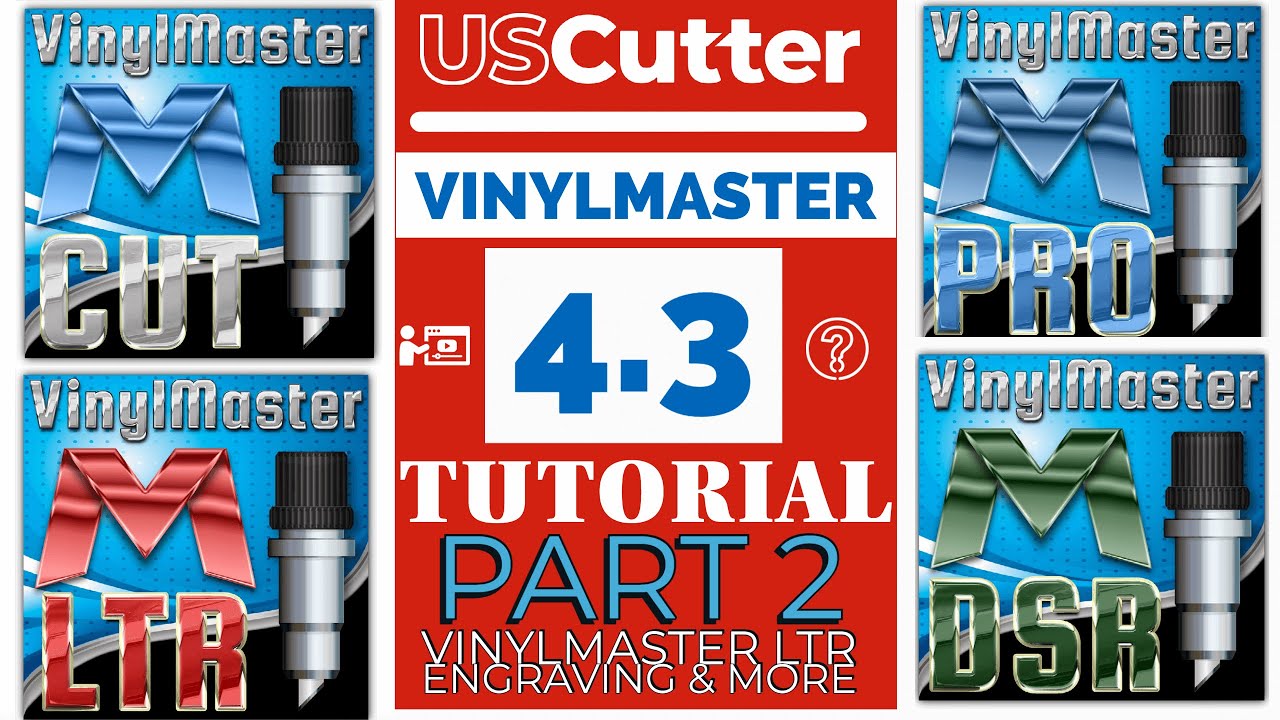
This allowed the vinyl to flow better in the pressing stage and reduced the non-fill problem. After separating from the master, a new mother was polished with a fine abrasive to remove (or at least round-off) the microscopic "horns" at the top of the grooves, produced by the cutting lathe. This also cleaned the surface of the matrix about to be copied. The electrolytic method was similar to the standard electrolytic cleaning method except the cycles were reversed finishing the process with the matrix as the anode. Soaking in a dichromate solution was another popular method, however, this method risked contaminating the nickel solution with chrome.
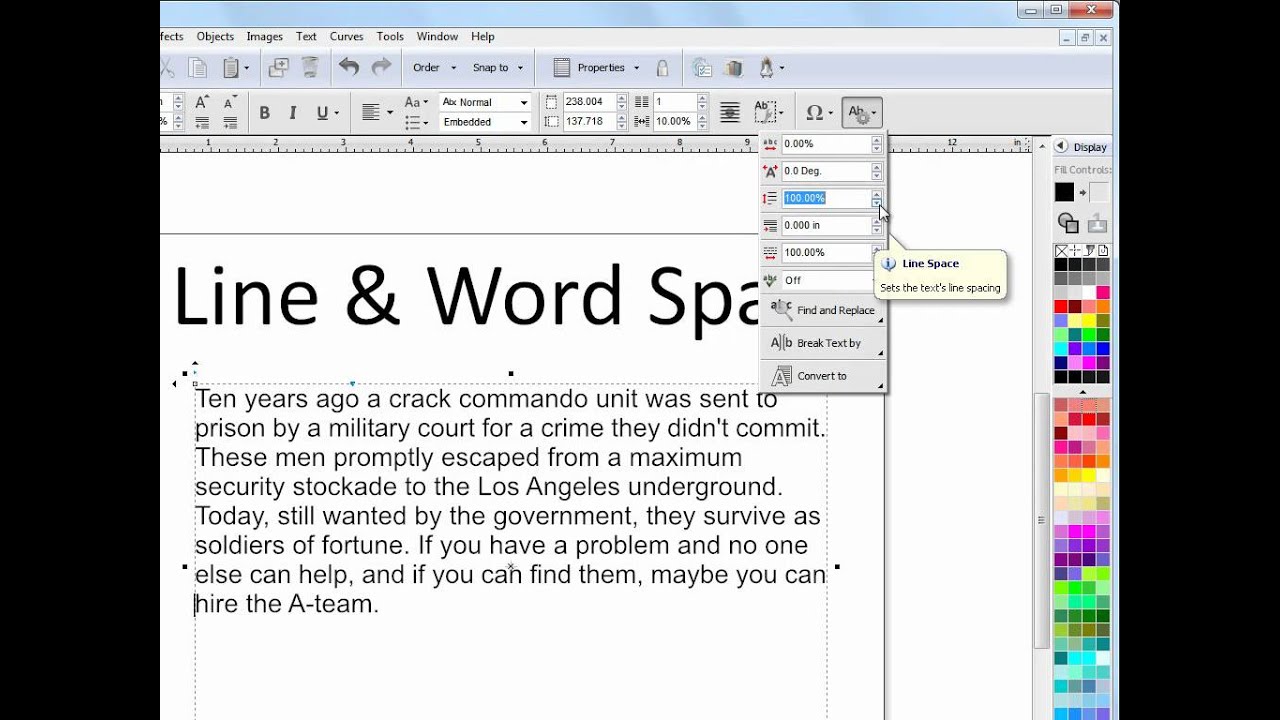
There were several methods used EMI favoured the fairly difficult albumin soaking method whereas CBS Records and Philips used the electrolytic method.
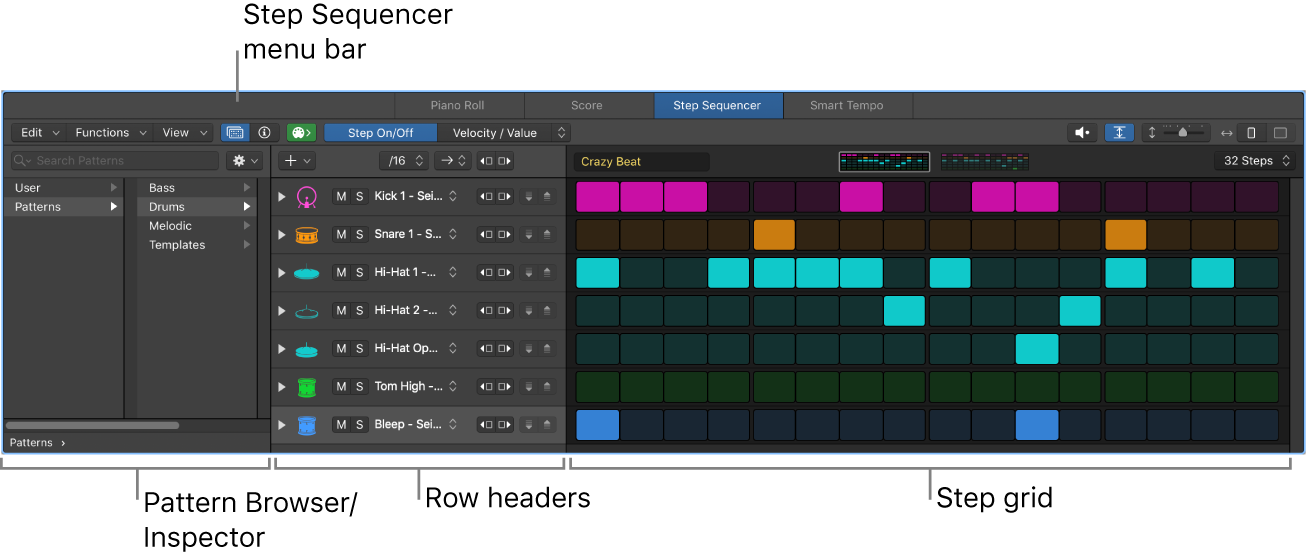
Prior to plating either the nickel master or nickel mother, it needed to be passified to prevent the next matrix from adhering to the mother.
#Erase lines on vinyl master pro full
Producing mothers was similar to electroforming Masters, except the time allowed to turn-up to full current was much shorter and the heavier Mothers could be produced in as little as one hour and stampers (145 grams) could be made in 45 minutes. From these positives, stampers (negatives) would be formed. In the earliest days the negative master was used as a mold to press records sold to the public, but as demand for mass production of records grew, another step was added to the process.Īfter removing the silver deposit and passifying (see below), the metal master was then electroplated (electroformed) to create metal positive matrices, or "mothers". (In the UK, this was called the master note the difference from soft master/lacquer disc above). When this metal master was removed from the lacquer (master), it would be a negative master or master matrix, since it was a negative copy of the lacquer. This and all subsequent metal copies were known as matrices. In this, the current would be raised at regular intervals until it reached between 110 A and 200 A, depending on the standard of the equipment and the skill of the operators. Most factories transferred the master matrix after an initial flash of nickel from a slow warm nickel electroplating bath at around 15 amperes to a hot 130 degree nickel plating bath. Later with advent of nickel sulfamate plating solutions, all matrices were plated with solid nickel. This was followed by copper plating, which was both quicker and simpler to manage at that time. In the early days of microgroove records (1940–1960), nickel plating was only brief, just an hour or less. This coating provided the conductive layer to carry the current for the subsequent electroplating, commonly with a nickel alloy. After another rinse, they were sprayed with a mix of the silver solution and dextrose reducer to create a silver coating. Later masters made of lacquer were sprayed with a saponin mix, rinsed, and then sprayed with stannous chloride, which sensitized the surface. To prepare the master for making copies, soft masters made of wax were coated with fine graphite. The original soft master, known as a "lacquer", was silvered using the same process as the silvering of mirrors.
